Laser and Material Interaction: The Keyhole Effect
1. Formation and Development of the Keyhole
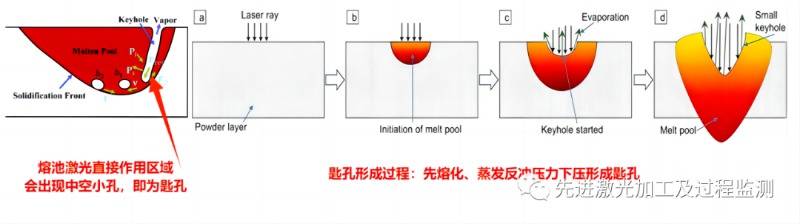
Definition of Keyhole: When the irradiance exceeds 10^6 W/cm^2, the material surface melts and evaporates under the influence of the laser. If the evaporation rate is sufficiently high, the vapor recoil pressure generated can overcome the surface tension of the liquid metal and gravity, displacing some of the liquid metal and causing a depression in the melt pool where the laser is acting, forming a small pit. The beam directly impacts the bottom of the pit, causing further melting and vaporization of the metal. The high-pressure vapor continues to force the liquid metal at the bottom of the pit towards the edges of the melt pool, deepening the hole further. This process continues until a keyhole-like small hole is formed in the liquid metal. When the pressure of the metal vapor generated by the laser beam inside the small hole balances with the surface tension and gravity of the liquid metal, the hole no longer deepens, resulting in a stable-depth small hole, which is referred to as the "keyhole effect."
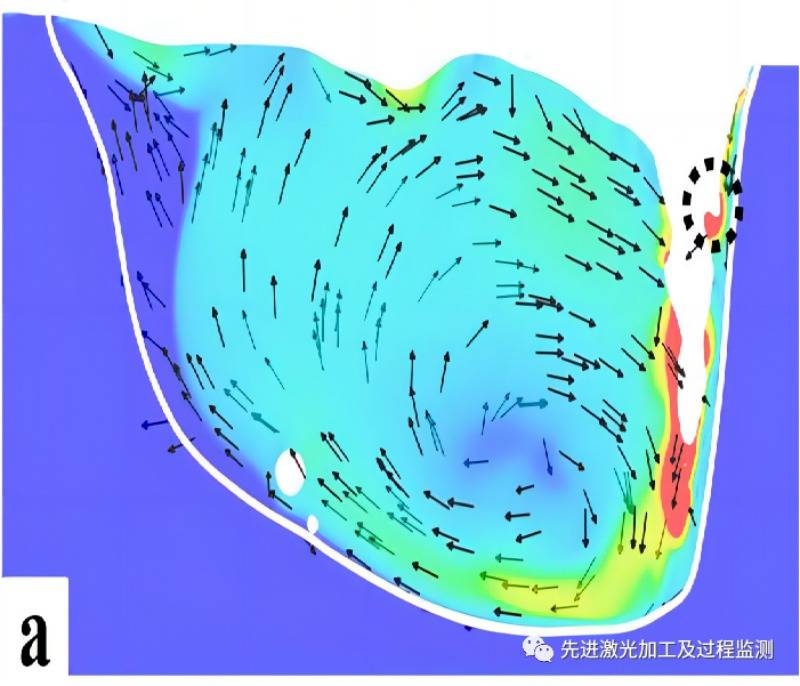
As the laser beam moves relative to the workpiece, the keyhole appears to bend slightly backwards at the front and tilts significantly in an inverted triangle shape at the rear. The front of the keyhole is the action zone of the laser, where the temperature is high and the vapor pressure is great, while at the rear, the temperature is relatively lower, and the vapor pressure is smaller. Under the influence of this pressure difference and temperature difference, the molten liquid flows around the keyhole from the front to the rear and forms a vortex at the rear end of the hole, eventually solidifying at the rear. The dynamic state of the keyhole obtained through laser simulation and actual welding shows the shape of the moving hole at different speeds and the situation of surrounding molten liquid flow.

Due to the presence of the keyhole, the laser beam's energy penetrates deeply into the material, forming a deep and narrow weld seam. The typical cross-sectional appearance of a deep penetration laser weld seam is shown. The depth of the weld seam is close to the depth of the keyhole (precisely speaking, the metallography is 60-100 µm deeper than the keyhole, a difference of one liquid phase layer). The greater the laser energy density, the deeper the keyhole, and thus, the deeper the weld seam. In high-power laser welding, the depth-to-width ratio of the weld seam can reach up to 12:1.
2. Analysis of Keyhole's Absorption of Laser Energy

Before the formation of the keyhole and plasma, the laser energy is mainly transmitted to the interior of the workpiece through thermal conduction, with the welding process falling under conduction welding (within a melt depth of 0.5mm), where the material's absorption rate of the laser is between 25-45%. Once the keyhole is formed, however, the laser energy is primarily absorbed directly by the interior of the workpiece through the keyhole effect, transitioning the process to deep penetration welding (with a melt depth greater than 0.5mm), and the absorption rate can exceed 60-90%.
The keyhole effect plays a crucial role in enhancing the absorption of laser energy during laser welding, cutting, drilling, and other processing techniques. The laser beam entering the keyhole is almost completely absorbed after multiple reflections off the keyhole walls. It is generally believed that the mechanism of laser energy absorption within the keyhole includes two processes: inverse Bremsstrahlung absorption and Fresnel absorption.
3. Energy Absorption in the Keyhole: Fresnel Absorption
Fresnel absorption is the mechanism by which the keyhole walls absorb laser energy, describing the absorption behavior of the laser's multiple reflections within the keyhole. Once the laser enters the keyhole, it undergoes multiple reflections off the inner walls, with a portion of the laser energy being absorbed by the keyhole walls during each reflection.
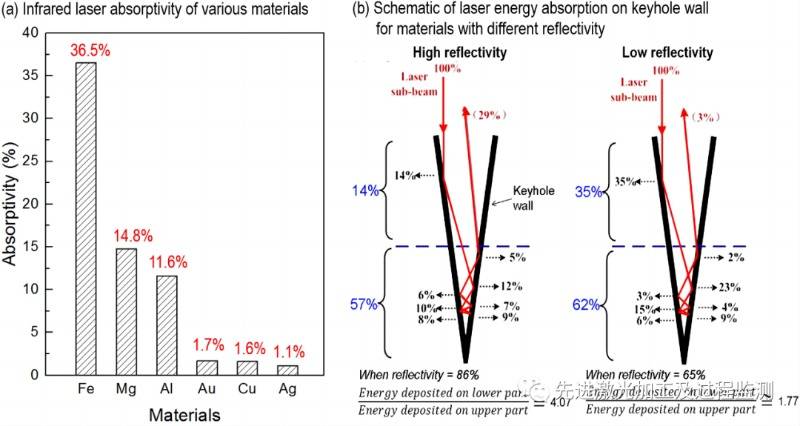
From the illustration, it is evident that steel's absorption rate for infrared lasers is approximately 2.5 times that of magnesium, 3.1 times that of aluminum, and 36 times that of gold, silver, and copper. For materials with high reflectivity, the multiple reflections of the laser beam inside the keyhole serve as the primary mechanism for energy absorption during the deep fusion laser welding process. The diagram for materials with different reflectivities shows that a low absorption rate results in a lower energy coupling efficiency for high-reflectivity material welding (71% vs. 97%), with a higher concentration of energy absorption at the bottom of the keyhole. In the process of welding high-reflectivity materials, the uneven distribution of energy along the depth of the keyhole accelerates its instability, leading to porosity, lack of fusion, and poor appearance.
4. Energy Absorption in the Keyhole: Inverse Bremsstrahlung Absorption

Another mechanism of energy absorption in the keyhole is through inverse Bremsstrahlung absorption by the plasma. Photo-induced plasma not only exists above the exit of the keyhole but also fills the entire keyhole. As the laser travels between two reflections off the keyhole walls, a portion of its energy is absorbed by the plasma. The energy absorbed by the plasma is then transferred to the keyhole walls through convection and radiation.
The roles and proportions of the two energy absorption mechanisms: The two mechanisms of laser energy absorption within the keyhole have different effects on the formation of the weld seam. The energy absorbed by the plasma is mostly released at the upper part of the keyhole, with less release at the bottom, leading to the formation of a "wine glass" shaped keyhole, which is not conducive to the expansion of the keyhole depth. On the other hand, the energy released by the Fresnel absorption at the keyhole walls is relatively evenly distributed along the depth of the keyhole, which is beneficial for increasing the depth of the keyhole, ultimately resulting in a deeper and narrower weld seam. From the perspective of improving welding quality and efficiency, controlling the plasma inside the keyhole for better welding stability is advantageous. Techniques such as laser modulation, adjustable ring mode, and composite heat sources are potential effective solutions.
5. Pressure Balance within the Keyhole
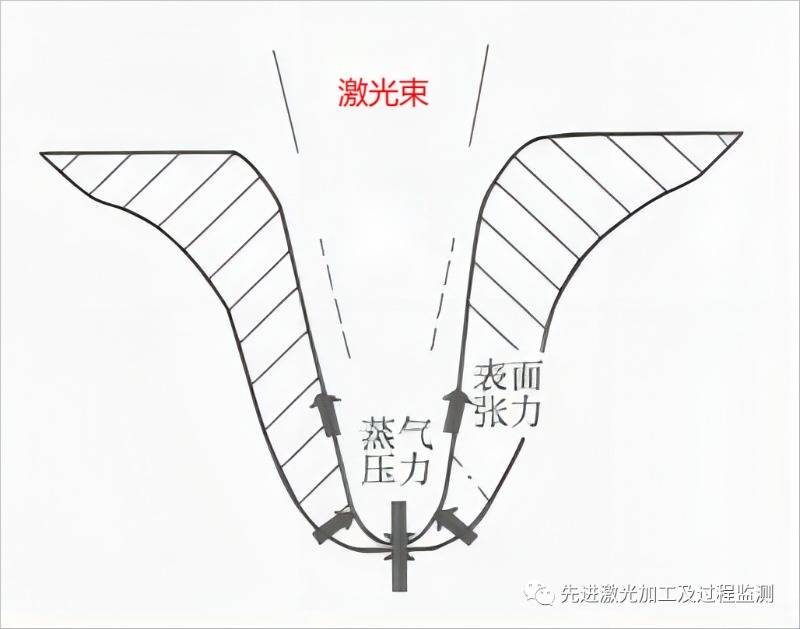
During deep penetration laser welding, intense vaporization of the material occurs, and the expansion pressure generated by the high-temperature vapor displaces the liquid metal, forming a keyhole. Inside the keyhole, there are several types of pressures present: the vapor pressure of the material, ablation pressure (also known as evaporative reaction force or recoil pressure), surface tension, hydrostatic pressure caused by gravity, and the dynamic pressure generated by the flow of the molten material. Among these pressures, only the vapor pressure acts to keep the keyhole open, while the other forces attempt to close it. To maintain the stability of the keyhole during the welding process, the vapor pressure must be sufficient to overcome the other resistances, achieving a balanced state and ensuring the keyhole's long-term stability. For simplicity, the forces acting on the keyhole walls are generally considered to be primarily ablation pressure (metal vapor recoil pressure) and surface tension.
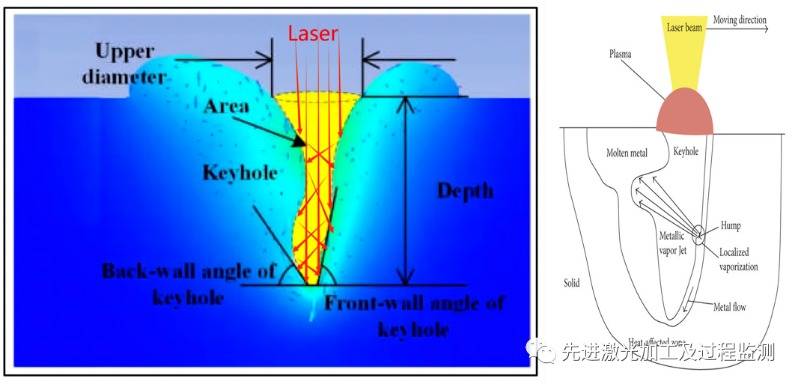
6. Instability of the Keyhole
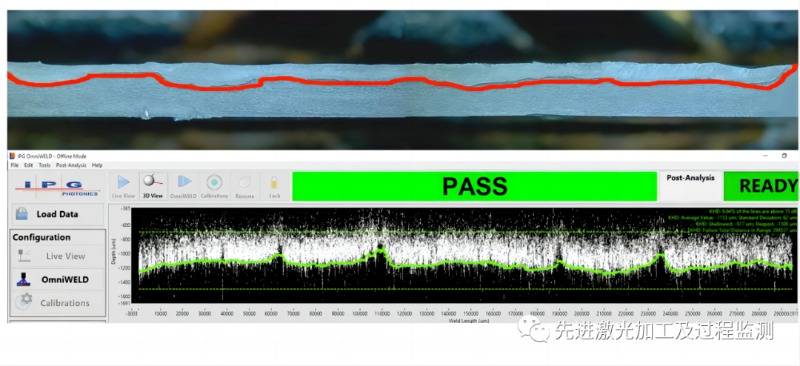
Wood engraving is a captivating and lucrative art form that has been revolutionized by diode laser engraving machines. Whether you're a DIY enthusiast or a small business owner looking to add a personal touch to your wooden creations, these machines can open up a world of possibilities. In this comprehensive guide, we will delve into the capabilities of diode laser engraving machines and explore five exciting projects that demonstrate their versatility.
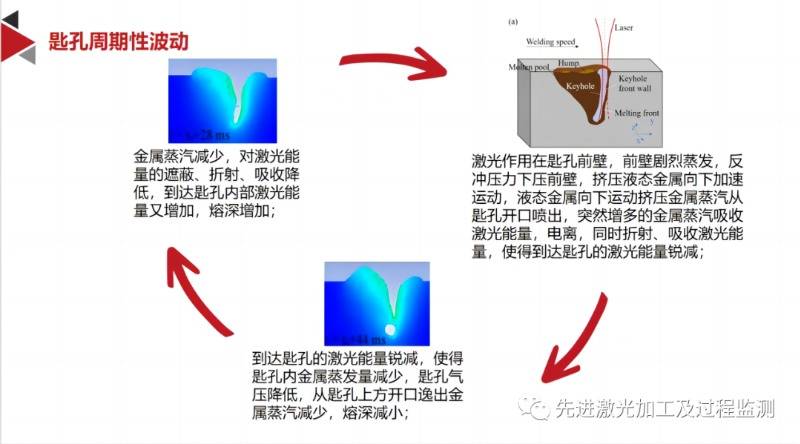
7. Directions for Improving Keyhole Stability
Wood engraving is a captivating and lucrative art form that has been revolutionized by diode laser engraving machines. Whether you're a DIY enthusiast or a small business owner looking to add a personal touch to your wooden creations, these machines can open up a world of possibilities. In this comprehensive guide, we will delve into the capabilities of diode laser engraving machines and explore five exciting projects that demonstrate their versatility.
8. How to Stabilize the Keyhole?
The fluid dynamics within the keyhole are complex, involving numerous factors such as temperature fields, flow fields, force fields, and optoelectronics, which can be broadly categorized into two groups: the relationship between surface tension and metal vapor recoil pressure. The metal vapor recoil pressure acts directly in the formation of the keyhole, closely related to the keyhole's depth and volume, and as the only substance in the welding process that moves upward, it's also closely related to the occurrence of spatter; surface tension, on the other hand, affects the flow of the melt pool.
Thus, stabilizing the laser welding process involves maintaining a steady distribution gradient of surface tension in the melt pool without significant fluctuations. Surface tension is related to the temperature distribution, which in turn is related to the heat source. Therefore, using a composite heat source and swing welding are potential technical directions for stabilizing the welding process.
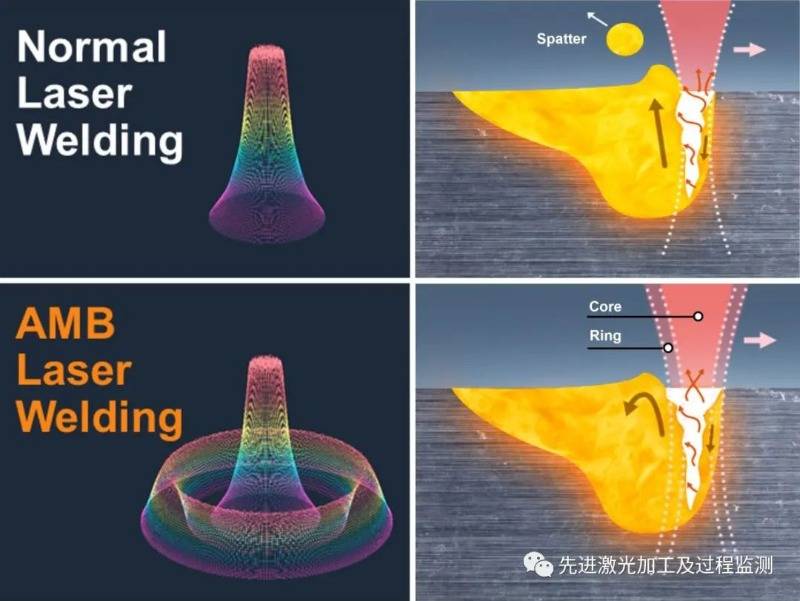
Attention should also be paid to the effects of plasma and the size of the keyhole opening. The larger the opening, the bigger the keyhole, making the fluctuations at the bottom of the melt pool relatively insignificant, which minimally affects the overall keyhole volume and internal pressure changes. Therefore, adjustable ring mode lasers (annular beam), laser-arc hybrid welding, and frequency modulation are viable directions for exploration.
Free SVG & Gcode Files for Laser Engraving & Cutting can be found here, wich you can import into our laser cutters directly.