Why Did We Choose CoS Packaging For Laser Engraver?
In the world of laser engraving, the choice of packaging technology is a critical factor that can significantly influence the performance and reliability of laser systems. Amid the diverse packaging solutions available, the adoption of 'Chip on Submount' (CoS) technology has emerged as a strategic decision for numerous reasons. CoS, with its unique blend of exceptional thermal management, mechanical resilience, and precise optical alignment, has risen as the preferred packaging solution for laser engraving applications. This article explores the key motivations behind the selection of CoS technology in the realm of laser engraving and how it is instrumental in shaping the capabilities and outcomes of this dynamic industry.
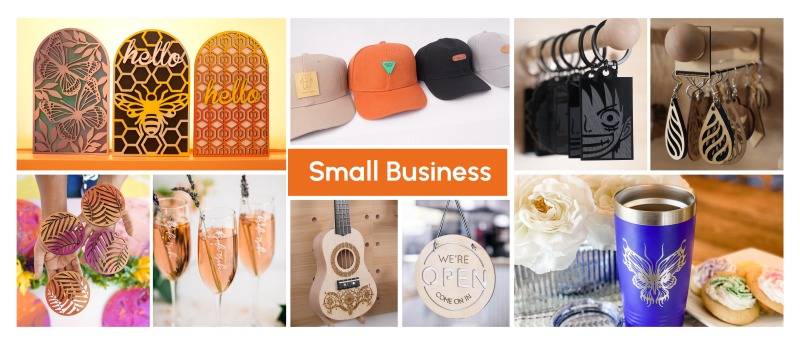
Blue laser, a new solution for desktop-level material processing
Blue diode laser(DL) material processing is based on the high photon energy of 450nm blue laser and the high brightness of the laser. By delicate optical design and coupling, a 0.15mm size blue laser spot with an energy of 5W to 40W is focused right on or a few millimeters beneath the surface of the material. The temperature increases immediately, burning and even vaporizing the material. Accompany by high-pressure air blowing, the oxidized material is blown away, creating beautiful engraving and cutting patterns.
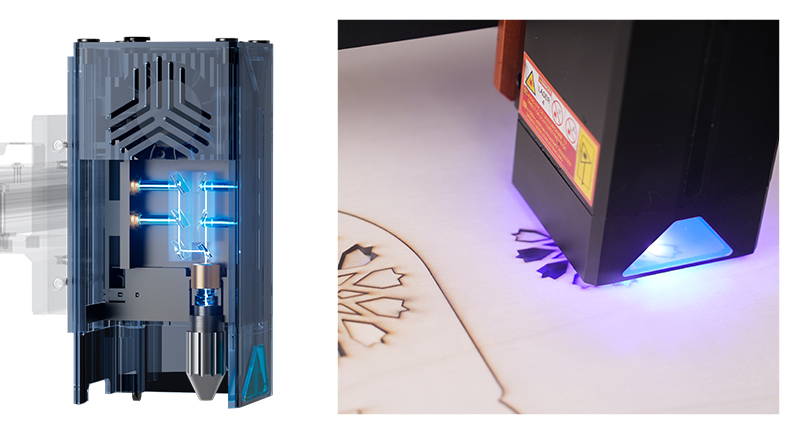
Figure 1. The schematic of blue laser engraving
Current blue DL can meet the demand of engraving or even cutting wood, leather, colored plastic, and steel. Compared to traditional CO2 laser applied for the same purpose, the more compact design blue laser has unique advantages for desktop material processing. Owing to its small size, low energy consumption, flexibility, and cost-effectiveness, blue DL material processing has more potential to replace traditional engraving and cutting methods.
·Free-space Output DL Device & Blue Laser Chip
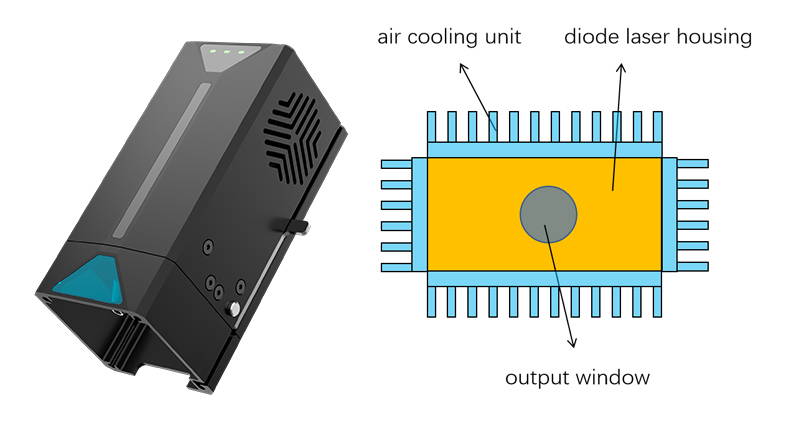
Figure 2. 450 nm blue laser module
A 20W Blue DL device, as shown in Fig. 1, normally includes a 20W blue DL module, an electric controlling unit, and an air cooling unit. As one single commercial blue laser diode (LD) can emit optical power up to 5W, it would take optical coupling of 4 diodes to output 20W. To ensure that the LDs work at the proper temperature range, the DL module is surrounded by air-cooling channels (cooling fins). The gap between these two units is filled up with the heat-conductive material (e.g., the thermally conductive silicone grease)
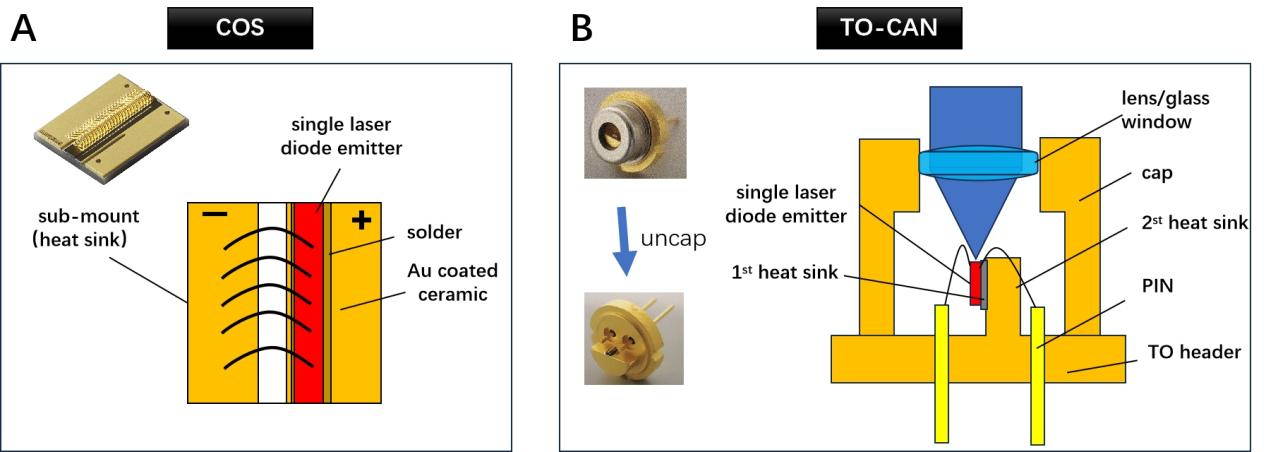
Figure 3. Blue diode laser packaging schematics (A) CoS package. ( B) TO-CAN package.
The diode laser engraver module packaging refers to the optical laser beam shaping, heat dissipation, and hermetic sealing of the laser diode. As the electric-optic conversion efficiency of the 5W blue LD is around 30%, 10W will be generated by the LD. For thermal stability and further packaging, the diode needs to be soldered onto a heat dissipation sub-mount, just as shown in Fig. 3 (A). The substrate material of the sub-mount not only has high thermal conductivity, but also a thermal expansion coefficient matching the diode. Ceramics such as AlN and SiC are usually used as the sub-mount substrate with both sides coated with layers of Ti/Cu/Au.
Except for the CoS package, another packaging style that is applied in the blue LD production is the TO-CAN package. As it is shown in Fig.3 (B), the diode is sealed in a metal can. In this case, the diode will be packaged twice, the first package is the CoS package, where the single LD emitter is soldered onto the 1st heat-sink, i.e., the sub-mount. Then the CoS is soldered onto the basis of the TO-header. Finally, the diode is encapsulated with a cap with a transparent window (lens of thin glass). The TO-CAN packaged blue LD is widely used in the illumination and projection area.
·Free Space Blue DL Module Package

Figure 4. The schematics of (A) TO-90 packaging and (B) CoS packaging.
The laser diodes that were first used for DIY blue laser engraving and cutting are packaged in terms of TO-90 (TO-CAN of 9mm outer diameter) as shown in Fig. 4(A). The reason why this kind of package is applied is due to the wide application of TO-CAN blue LDs in the projection and illumination area, where the output power of the whole DL module is small and the brightness of the laser beam is relatively low. Taking 20W blue DL module for example, 4 pcs of TO-CAN LDs shall first be uncapped so that the optical coupling can proceed. After the vertical-axis optical coupling, the uncapped TO-CAN will be re-capped. After that, the TO-CAN diodes are usually glued to the metal housing for the rest optical coupling. At last, the whole package is glue-sealed. Taking the CoS as the preliminary package, the diodes are packaged triple times in this TO-CAN-based blue DL module.
Compared to the TO-CAN packaging solution, the manufacturing process of the CoS solution is simpler. As it is shown in Fig. 4(B), the CoS LDs are soldered onto the copper housing. After delicate optical coupling, the LDs and optical lenses are sealed with parallel seam sealing and glass soldering techniques.
Due to different packing strategies, theoretically, the CoS packaged module has better air tightness compared to the TO-CAN packaged module. With seam sealing and glass soldering, the CoS module can achieve atom-level hermetic sealing. TO-CAN packaged module, on the other hand, is non-hermetic sealing, where optical lenses are vulnerable to invading humidity if the module operates in a highly humid environment.
As for thermal stability, the heat created by the chip is dissipated along a shorter path in the CoS LD packaged module. The diode chips are packaged only twice. The soldering material that fixes CoS onto the copper housing is solder alloy with a thermal conductivity from 20 to 60 W•m-1•K-1, while TO-CAN LDs are attached to the metal housing with the glue. The thermal resistance of the CoS module is lower, which brings better heat dissipation capability.
The combined effects of these elements will result in the differences in the reliability of these two different packaging strategies. CoS solution has advantages in terms of production simplicity, air tightness, and heat dissipation capability.
·Life-time Test of Blue CoS Modules
Considering the higher air tightness and heat dissipation capability, the reliability of the CoS-packaged DL module is theoretically better in terms of long-term operation. Normally in the industrial laser area, the CoS has been considered a better solution for the high power DL packaging. The blue DL single module output 250W based on the CoS solution has been reported.

Figure 5 .The lifetime test of the 60W fiber output blue DL module (A) and the 20W free space output DL module (B).
X Photonics specializes in high-power diode laser technology, aiming to build consumer-electronics-level blue DL products with industrial reliability standards. The lifetime test data of the fiber output DL modules and the free space output DL modules, as shown in Fig.5, prove that the CoS-packaged DLs have good long-term operation performance. The average optical power drop of the 60W fiber output module is less than 2% after operating 800hrs. As for the free space output DL module with a much more compact design, the average optical power drop of 19 pcs 20W modules is less than 10% after 1800 hrs aging. The reliability data of different produced patches will continue to be collected for more scientific and statistical proof of the CoS modules.
Conclusion
In conclusion, The total cost of ownership (TCO) of the CoS solution is better, even though the corresponding current cost might be slightly higher. Better air tightness and thermal stability endow blue CoS DL modules with unique advantages for high-power DL packaging. With the expanding consumer electronics and industrial application market, the price of the blue CoS LD will keep on declining as its manufacturing scale grows. The long-term TCO of the CoS solution is more competitive, and Algolaser along with X Photonics will keep on the development and iteration of the high-power blue COS-based diode laser modules and systems.