How to Fix the Crashing Sound of the Alpha MK2 Laser Engraver
1. Introduction to the Problem
When you switch on your Alpha MK2 laser engraver and initiate the homing process, you may sometimes hear a knocking sound emanating from the machine. This noise, typically from the left side, can be alarming and signals that something is not functioning correctly. The primary cause of this issue is often that the limit switches are not being triggered correctly due to an uneven X-axis, where the gantries are not parallel.
The X-axis is crucial for accurate engraving and cutting, as it controls the movement of the laser module across the material. If the gantries on the X-axis are not parallel, the laser module may not move smoothly, resulting in misalignments and the dreaded knocking sound. Addressing this issue promptly is essential to maintain the precision and efficiency of your laser engraver.

2. Initial Steps: Emergency Stop and Preparation
The first step when you notice the knocking sound is to immediately press the emergency stop switch. This action halts the machine’s operations and prevents further potential damage. Once the machine has stopped, unplug the cable to ensure it is entirely powered down and safe to work on.
Before proceeding with any adjustments, gather the necessary tools. The most important tool you will need is a set of socket head cap screws, typically found in the tool kit provided with your laser engraver. Having these tools on hand will make the adjustment process smoother and more efficient.
With the tools ready, you can begin the process of adjusting your laser engraver to eliminate the knocking sound and restore smooth operation.




3. Adjusting the Front Tension Screws
To start adjusting the machine, begin by addressing the front tension screws. These screws control the tension of the belts that move the gantries along the X-axis. Improper tension can lead to uneven movement, which is often the root cause of the knocking sound.
Start by unscrewing the front tension screws. This will allow you to adjust the tension to the correct level. As you unscrew, secure the inner side of the gantry with your other hand to prevent it from shifting. Then, twist the tension screws in the “+” direction to increase the tension.
After adjusting one side, repeat the same steps on the opposite side. Ensuring both sides are evenly tensioned is crucial for maintaining parallel gantries, which in turn ensures smooth and accurate movement of the laser module.




4. Removing the Y-axis Couplings
Next, you will need to remove the two couplings on the Y-axis. These couplings connect the Y-axis motor to the belts that drive the gantry along the Y-axis. Removing these couplings allows you to make necessary adjustments to the gantry alignment without interference from the motor.
Carefully unscrew and remove the couplings. With the couplings removed, you can manually move the gantry and ensure that both the left and right ends contact the limit switches simultaneously. If one side reaches the limit switch before the other, it indicates that the gantries are not parallel and need adjustment.




5. Assessing the Gantry Push Resistance
With the couplings removed, the next step is to assess the resistance of the gantry on both sides. Push the left and right sides of the gantry separately to feel the difference in resistance.
For example, if the left end moves easily with just a little force, but the right end offers significant resistance, it suggests that the gantries are not aligned correctly. This imbalance in resistance can cause the knocking sound and may also lead to uneven engraving or cutting.
Understanding the level of resistance on each side will guide you in making the necessary adjustments to the eccentric nuts and other components.



6. Adjusting the Eccentric Nuts
Now it’s time to adjust the eccentric nuts. These nuts are located on the underside of the gantry and are responsible for adjusting the tightness of the wheels that run along the rails.
Start by unplugging the cables associated with the laser module and carefully removing the module. This step is necessary to access the eccentric nuts and make the adjustments without damaging the module.
Place the machine upside down to expose the eccentric nuts. The nut on the side with higher resistance (the hard push side) is likely too tight. Use a wrench from your tool kit to loosen this nut slightly. Adjust the tightness of the nut until it feels like there’s a fair amount of slack, but not too loose.
At the same time, ensure that the adjacent eccentric nuts are tightened in the opposite direction. This counterbalance helps maintain the proper tension and alignment of the gantry.






7. Reassessing the Gantry Push Resistance
After adjusting the eccentric nuts, it’s time to reassess the gantry push resistance. Push the left and right sides of the gantry again to check if there’s now even resistance on both sides.
If the adjustments were successful, the right side should now move as easily as the left side. The knocking sound should be gone, indicating that the gantries are now parallel and the limit switches are being triggered correctly.

8. Reinstalling the Components
With the gantry adjustments complete, you can begin reinstalling the components. Start by reinstalling the coupling on one side of the Y-axis. Align the two shaft gaps with the centerline of the coupling to ensure proper alignment.
Next, push the gantry to the top of its range. Then, tighten the coupling on the right side, making sure it is also aligned correctly. Finally, tighten the tensioner and check the belt tension by popping the belt. It should feel tight but not overly so, ensuring smooth movement of the gantry.


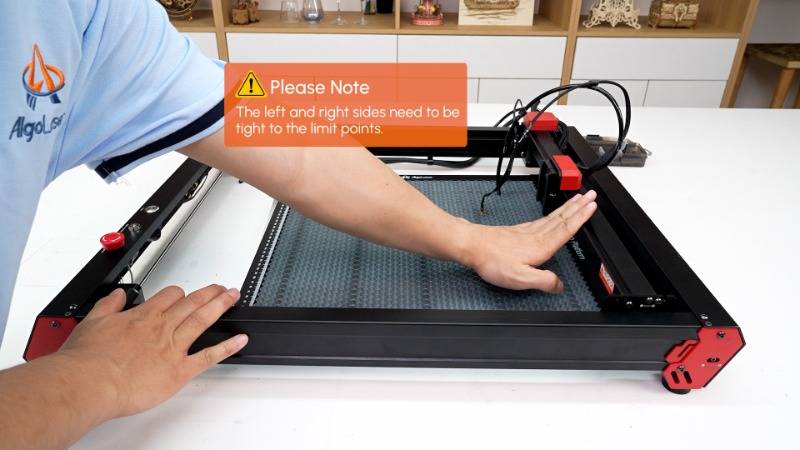


9. Final Checks and Power On
Before powering the machine back on, perform a final check to ensure consistent looseness on both the left and right sides of the gantry. This step is crucial to confirm that all adjustments were made correctly.
Once satisfied with the adjustments, reinstall the laser module and reconnect all associated cables. Power on the machine and perform a homing sequence. The machine should now operate smoothly without the knocking sound.
If the problem persists, revisit the steps and make further adjustments as needed. However, if the machine runs smoothly, you can proceed with your engraving and cutting projects with confidence.

10. Conclusion and Best Practices
Solving the knocking sound issue caused by an uneven X-axis on the Alpha MK2 laser engraver is essential for maintaining the machine’s precision and longevity. Regular maintenance, including checking the tension of belts, adjusting eccentric nuts, and ensuring the gantries are parallel, will help prevent this issue from recurring.
In conclusion, keeping your laser engraver in optimal condition requires attention to detail and a willingness to perform routine checks and adjustments. By following these steps, you can ensure that your Alpha MK2 operates smoothly, providing accurate and high-quality engraving and cutting results.
Remember, a well-maintained laser engraver is the key to successful projects and a longer-lasting machine.